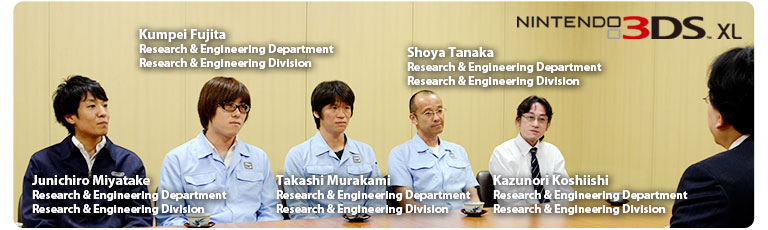
Nintendo has published a new Iwata Asks that provides a ton of insight into the creation process of the 3DS XL. The staff behind the project discuss how the project was initiated, challenges that came about, and more.
Satoru Iwata, Junichiro Miyatake, Kumpei Fujita, Takashi Murakami, Shoya Tanaka, and project leader Kazunori Koshiishi participated in the interview.
A summary of the discussion can be found below. For the full interview, check out this link.
A Size with Impact
– Talk of the 3DS XL began when Koshiishi’s department asked in an internal meeting, “Can we bring out the XL in 2012?”
– First idea was to make a working model with big LCDs
– A working model can function, but design and structure weren’t considered
– 4.88-inch top screen was decided in the working-model stage
– Wanted a big screen from the start because they wanted an impactful size for showing the 3D
– Size was determined based on the balance between cost and size
– Murakami: “As Koshiishi-san said, when it came to the LCD, size generally equals cost—it has a direct effect—but that doesn’t always mean that bigger is simply more expensive. The cost gradually changes depending on what size you cut from a single giant sheet of glass called the mother glass.”
– At that size, Iwata says it would be impossible to make a product under $200 a few months ago
– The team was able to pull it off by trying new things
– This includes “secrets” that Murakami can’t talk about
– Cost could be lowered due to mass production
– Cooperating manufacturer let Nintendo use their special factory facilities for large-screen liquid-crystal televisions
– This was the first time Nintendo attempted something like this
– Larger LCD screen caused a lot of challenges
– Iwata: “The first thing that I thought of was how a larger LCD would increase the area that the backlight needed to hit, thereby increasing power consumption. The casing is larger, so you might be able to handle it by increasing battery capacity, but you can’t just simply make it heavy either.”
– New, as-yet-unestablished technology for decreasing power consumption was discovered
– The tech holds down power consumption
– Compared to the original 3DS, it improved the use efficiency of light from the backlight
– Iwata: “When you view 3D images on the Nintendo 3DS, the liquid-crystal barrier blocks the images for the left and right eyes from each other, so the efficiency of the light is halved. You thought that improving that would also save power.”
– A parts maker made a new method for improving transmittance
– New tech didn’t exist when Nintendo was developing the 3DS
– The team made fine adjustments up to the end of the project
– LCD specs weren’t finalized until the end of 2011, even though they should be set early on
– Spending that time allowed Nintendo to solve the screen brightness and battery life issues
– Dots are smaller than on the DSi XL, but most players shouldn’t notice this
– Murakami: “To get a bit technical, it is thought that you need the screen to have at least 100 ppi to view good 3D images, and I’ve set it as a goal. What’s more, the Nintendo 3DS XL’s attraction as a product is that it’s bigger than the Nintendo 3DS and shows 3D graphics with impact—and when it comes to that, it’s just fine.”
Like Making a Puzzle
– Iwata was surprised that the 3DS XL’s LCDs are very narrow compared to previous Nintendo hardware
– Speakers influenced the frames’ design
– First design picture shown to the design team wouldn’t allow the same speaker from the original 3DS to fit
– Fujita: “As much as possible, we wanted to achieve what was pictured, so we searched for small speakers, and considered moving the speakers to the bottom half. We modified the DSi XL and put the speakers by the buttons, and checked how it sounded by listening to the opening theme music from Dragon Quest.”
– A number of speaker makers introduced a variety of technologies
– Nintendo heard about some thinner, elongated speakers rather than round ones
– While these speakers weren’t practical at first, they would really put out sound, so they thought they just might work
– A lot of research was done along with the manufacturer
– Eventually came up with the speakers that were used on the final product
– Custom-sized speakers were made to fit within a limited, narrow space
– Fujita: “On a graph of acoustic characteristics, they aren’t exactly identical to the Nintendo 3DS speakers. The speaker size is smaller than that of the ones on the 3DS so sonically it had a disadvantage. But by fine-tuning the structure and capabilities of the speakers itself, and then optimizing the sound with the software, we tried to have them sound like the ones on the 3DS as closely as possible.”
– Miyatake: “Adding to what we said about the frame, we made the base color black for everything on the Nintendo 3DS in order to accent the stereoscopic 3D. But the screen this time is big enough that the size alone can really immerse you, so we could use coloring besides black.”
– Resin is important when making a system as a whole thin
– Nintendo is using a thin resin that’s hard and provides good protection
– Surface material of the upper side when you open the 3DS features a new resin called nylon GF55
– GF is glass fiber
– It’s a plastic reinforced with fine glass fiber
– GF55 – 55% glass fiber
– Miyatake: “Usually, you bring out the color of the resin and then paint on it to draw out nice colors, but with GF resin, the original coloring doesn’t come out well.”
– Machining and decoration get difficult with 55% glass fiber
– Normal processes don’t work
– You spray on paint to serve as a nice base color, and then spray on a second coat for decoration
– Some aspects were completely rethought like clearance when assembling the various elements, performing incredibly detailed simulations for tolerance analysis
– Clearance is the space for parts to move
– Iwata: “And tolerance, since it is nearly impossible when mass producing parts to make everything exactly the same size as in the designs, is a value you decide on, saying, “This much is acceptable.” When assembling numerous parts, that difference could have an effect on the whole thing, so tolerance analysis is calculating ahead of time to make sure that doesn’t happen.”
– If each piece has tolerance, every little difference could add up to a lot
– A lot of talk about things like “Can we make this 0.1mm smaller?”
Good but Inexpensive
– When he first saw the working model, Miyatake was surprised and thought the project would go well
– Although the 3DS XL LCD is bigger, the thickness hasn’t changed much
– The website lists the XL as being 22mm thick, but it includes the feet-like projections
– Without it the thinnest part is 21.3mm
– That’s only 0.1mm more than the 3DS
– Size measurements are close to the DSi XL, but it seems pretty small when compared side-by-side
– Miyatake: “We designed it with the concept ‘A softer 3DS with a bigger screen’. It was only made possible because it was a larger piece of hardware, but the battery is in the center of the main body this time, so we could achieve more rounding on the exterior surfaces than ever before. With the battery in the center, the balance of weight is good.”
– New method for adding decorations to the exterior was attempted
– Miyatake: “We did, in order for people to be able to casually carry it around like they are doing with the 3DS, we thought first and foremost of a neutral design, one without much difference between the top and the back of the system. We looked at ways we could give it variation by changing the colors and patterns of the exterior. A big point design-wise in allowing it to have those variations was the method of decoration. We looked at various methods and technologies, but based on cost and marketability, we ended up adopting IMD.”
– IMD is a method of molding using film
– IML was used for the 3DS
– IMD and IML are both film molding
– In IML, the film remains as a protective layer on the surface
– In IMD, the film is removed in the end
– IML in the 3DS had an advantage toward forming three-dimensional shapes compared to IMD
– Nintendo had used IMD for the Game Boy Micro face plat and the Pokewalker
– A manufacturer introduced IMD tech to Akai and Murakami a little before the project started
– Akai liked it and often pushed to use IMD
– Akai favored IMD since it’s easier to apply various colors with a single foil sheet compared to painting
– Fewer defects arise as a result
– It increases yield and decreases man-hours
– IMD is better since the colors are already in place with the film printing and the UV protective layer is on the surface from the start
– This makes it better from a cost perspective
– Didn’t go smoothly after IMD was settled on
– Film is thin, so on the black where you pour in the resin, the film would run and warp
– Resin causes it to warp
– Fujita: “Yes. It was a specific method, so all sorts of problems arose during the testing phase. We had the manufacturer come to the factory in China and observe the problems, and for film design, thought about bending it ahead of time in expectation of distortions during mass production. We were discussing it until about two weeks before mass production began and somehow made it in time.”
– The team wanted to give users something good but inexpensive
– Miyatake put estimated costs up alongside the various proposals starting with the first approval of the design
More Than Just Bigger
– For software, Tanaka wanted the XL to be as identical to the 3DS as possible
– Also wanted to not place a burden on game developers
– The same software has to run smoothly on the system so that game developers and gamers don’t notice any differences
– Some things had to change
– They tried to make appropriate adjustments to keep those things to a minimum
– A lot surrounding the 3DS XL project was initially still a secret, even inside Nintendo
– Keeping all that in the dark while moving forward was hard for Tanaka
– Some graphics changed with the XL
– Ex: explanations for the players about hardware features, like where to place the stylus and where to insert the SD card
– SD Card slot is now on the right side and not the left
– Stylus is removed from the side now
– Stylus material also changed
– A big change was the click for the 3D Depth Slider
– There’s a click when you switch from 3D to 2D
– Tanaka: “It’s the same system as the 3DS, so aside from the click, we adjusted the various values of each process so it would run the same.”
– This requires adjustments between a lot of departments
– Email was mostly used since others will be able to hear if you talk over the phone
– The team knew about possible structural weaknesses and where applying pressure was likely to break the system
– The design data was simulated first
– This was armed with certain estimates and the team checked as they went
– After narrowing down things somewhat, prototypes were made and fine-tuned
– In the 3DS XL simulations, the team paid attention to the hinge supporting the top screen’s weight
– Weight of the casing on the upper side that need to be supported increased, so the hinge has roughly twice the torque compared to the original 3DS
– That much strength was necessary to make sure that the upper half wouldn’t fall over
– Making something stronger could make it easier to break
– Samples were taken to the Repair and Maintenance Center and Customer Service Office
– The employees there looked at the prototypes, tried them out, and repeatedly fine-tuned them in degrees of one newton centimeter
– Support of the hinge pin wasn’t strong enough with the existing design
– Fujita created a separate part made of special plastic
– They were able to achieve high torque while saving space
– To increase strength, they beefed up design review and ran simulations
– Murakami: “We gathered specialists in various fields and examined the designs before making the trial models. We explained our designs, had the specialists raise concerns, and then reflected those concerns in the designs. We did that more often and earlier this time.”
– Cooperative work between the development design department and the section in charge of manufacturing earlier than before
– They also wanted early opinions from the Repair and Maintenance Center and Customer Service Office
– There was some debate about the battery cover
– Ex: whether or not there should be screws, their placement, shape of the fingerhold
– Since the Repair and Maintenance Center and Customer Service Office hear a lot of comments from customers, they can give real advice
– Miyatake: “Yeah. At first, there was a projection on the battery cover. That made it easy to remove, but it’s at a place where it could be obtrusive when using the L and R Buttons, and there were concerns that people may try to remove the cover before they remove the screws. So we were like, ‘That just won’t do!’ (laughs) …So we took in all kinds of samples without projections, and eventually settled on one of those designs after putting in consideration about how often it would actually be removed.”
– There were other changes along the way
– Nintendo’s contracting factory in China assisted with a lot of things such as assembling the metal mold and the coloring
– Iwata: “The more I hear what you have to say, the more I realize that this was about a lot more than just making it bigger. When the screen is 90% bigger and it weighs about 40% more, a lot has to be reconstructed. It’s not just the hardware development department, but many other departments and participating companies are involved from an early stage.”
Every Little Improvement
– Miyatake wants players to look at how some aspects of operation have been improved
– A, B, X, Y buttons and +Control Pad are bigger and thicker
– This makes them easier to use
– The thickness of the key tops height-wise for the L and R buttons were increased
– Miyatake had the designers work hard to have the Start, Select, and Home buttons in a way that the keys sink in a seesawing action
– These buttons have a long and think key top
– When you press them, they sink right in
– Miyatake: “And compared to past devices, the feeling of size when you hold it, as well as the impression it makes when you open it, are quite different from our past devices. Even though it’s big, you don’t sense that. I hope people will carry it around and play it everywhere.”
– Fujita made prototypes just for the Home, Select, and Start buttons and was really dedicated to them
– This was Fujita’s first product since moving to the Research & Engineering Department, so he was really attached to the project
– There’s a screen cover over the LCD screen
– A LCD screen has three reflective layers
– They all reflect and cause glare
– Nintendo specially treated the layers
– Reflectivity on the 3DS was roughly 12%, but with the XL, it’s about 3%
– Progress of technology made this possible
– Nintendo has been thinking about anti-reflection since the GBA, but usually had to give up due to cost
– The company had been keeping an eye on the tech the whole time
– The 3DS XL beats all previous Nintendo game systems in terms of anti-reflection
– Tanaka: “I wasn’t very involved with the hardware, but I think the 3DS XL’s best selling point is that the larger LCD increases parallax, so players can enjoy stereoscopic 3D with greater impact. The 3D Depth Slider has more range, making it easier to adjust to your own preferences, so I hope its good aspects will reach a broader range of people.”
– A video is pre-installed on the 3DS XL for experiencing 3D
– This video is a CG movie that Nintendo made drawing upon 3D knowhow gained from the 3DS
– At one point, the team considered making a new AC adapter
– Iwata: “According to the original specifications, if you were playing while charging, you were surpassing the capacity of the existing AC adapter. For that reason, there was a time that, you thought you might have to prepare a special version.”
– After cooperating with the manufacturer, they were able to get by with the existing adapter
– Cost was being discussed, as well as whether or not they needed to include the charging cradle
– Iwata suggested not including the AC adapter
– Koshiishi: “We worried over it, but during that time, all the groups within the company naturally shared a desire to separate what was absolutely necessary and what wasn’t. In the end, we decided that it was best to sell the AC adapter and the charging cradle separately.”
– Iwata: “About the AC adapter, this is the fourth of this type since the Nintendo DSi system, so I think many people have the previous AC adapters. That being the case, we thought we should make it easier, even if just a little, to buy the system. However, you have to have the stores notify shoppers that this product doesn’t come with an AC adapter, so if you don’t already have one, you have to buy it separately. This project required the sales division to be thorough on that point as well.”
– Iwata: “I agree. I, too, am truly looking forward to people’s reactions when it goes on sale. The best way to truly get a feel for the Nintendo 3DS XL’s features is to get your hands on and check out the actual thing. By the time this session of “Iwata Asks” goes live, a number of stores around the country will probably have started to install some on display, so if those reading this interview are interested, be sure to head on over to a game shop and try out an actual system!
“As a final comment, listening to you developers today, I strongly feel that we were only able to reach this point through the accumulation of many small efforts along the way. I realized all over again how hardware comes together when you have people who are always on the lookout for technology to use in the future and people who always want to make even the smallest improvement, and while that’s all just a matter of course for each individual, that dedication builds up.
“Good job, everyone. Thank you.”